Flow Tongs
This project deals with the methodologies for the generation of forms with complex transitional surfaces. The goal was to create two wooden forms that act as salad tongs.
Exploration
I began with some freeform sketching of silhouettes—I tried to explore a breadth of dynamic shapes while remaining considerate of ways the hand could comfortably grip the form. I then started to refine them by drawing inside the confines of the 10" x 1.875" x 3.25" wood block profiles.
For my first iteration in modeling foam, I chose a the following design; I felt it had an energy to it, yet was still simple enough to constitute a "flow form". I made the four cuts indicated in the template using a bandsaw, and then sanded the form smooth. For this iteration, I held off on doing any secondary shaping.
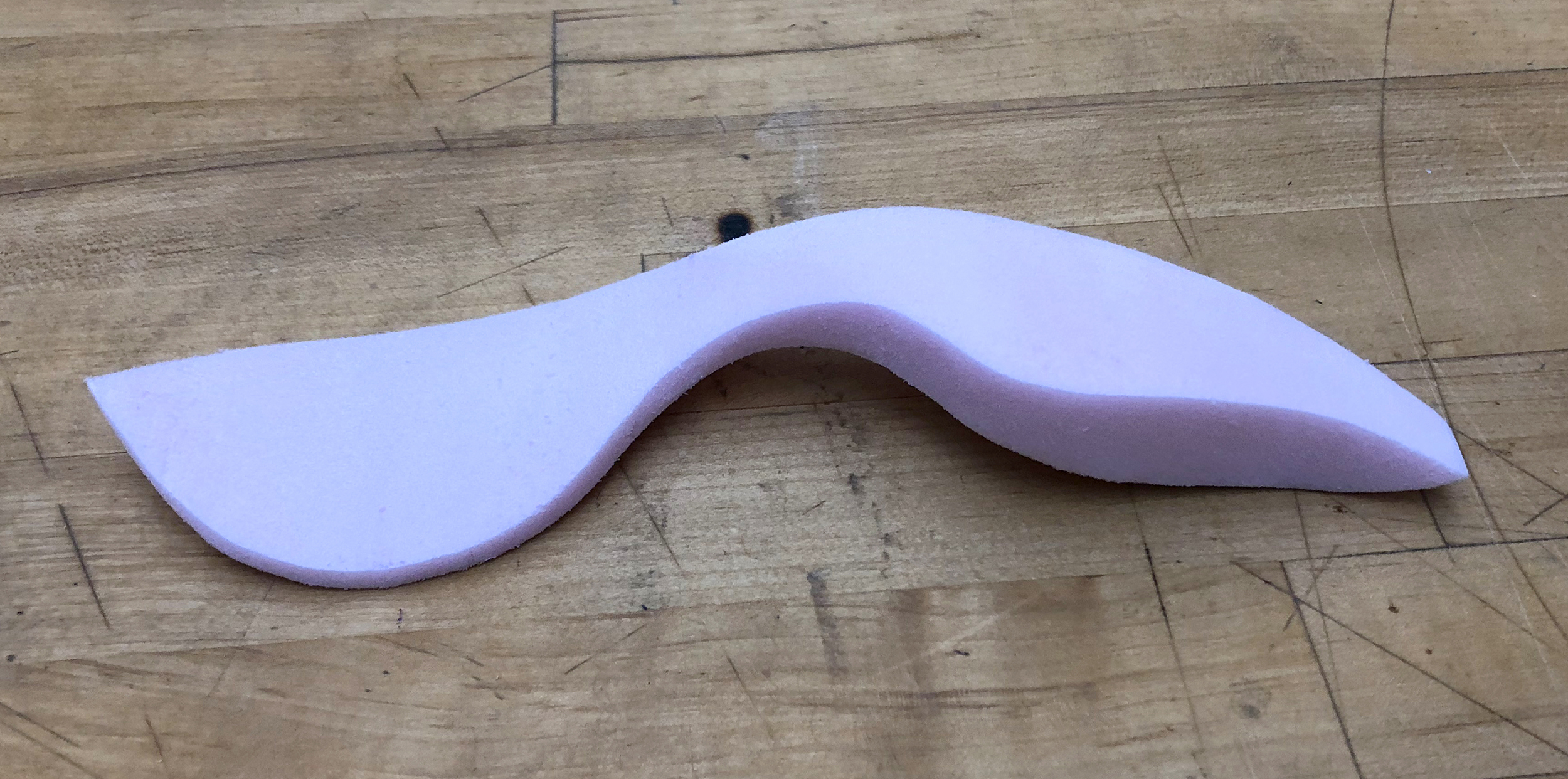
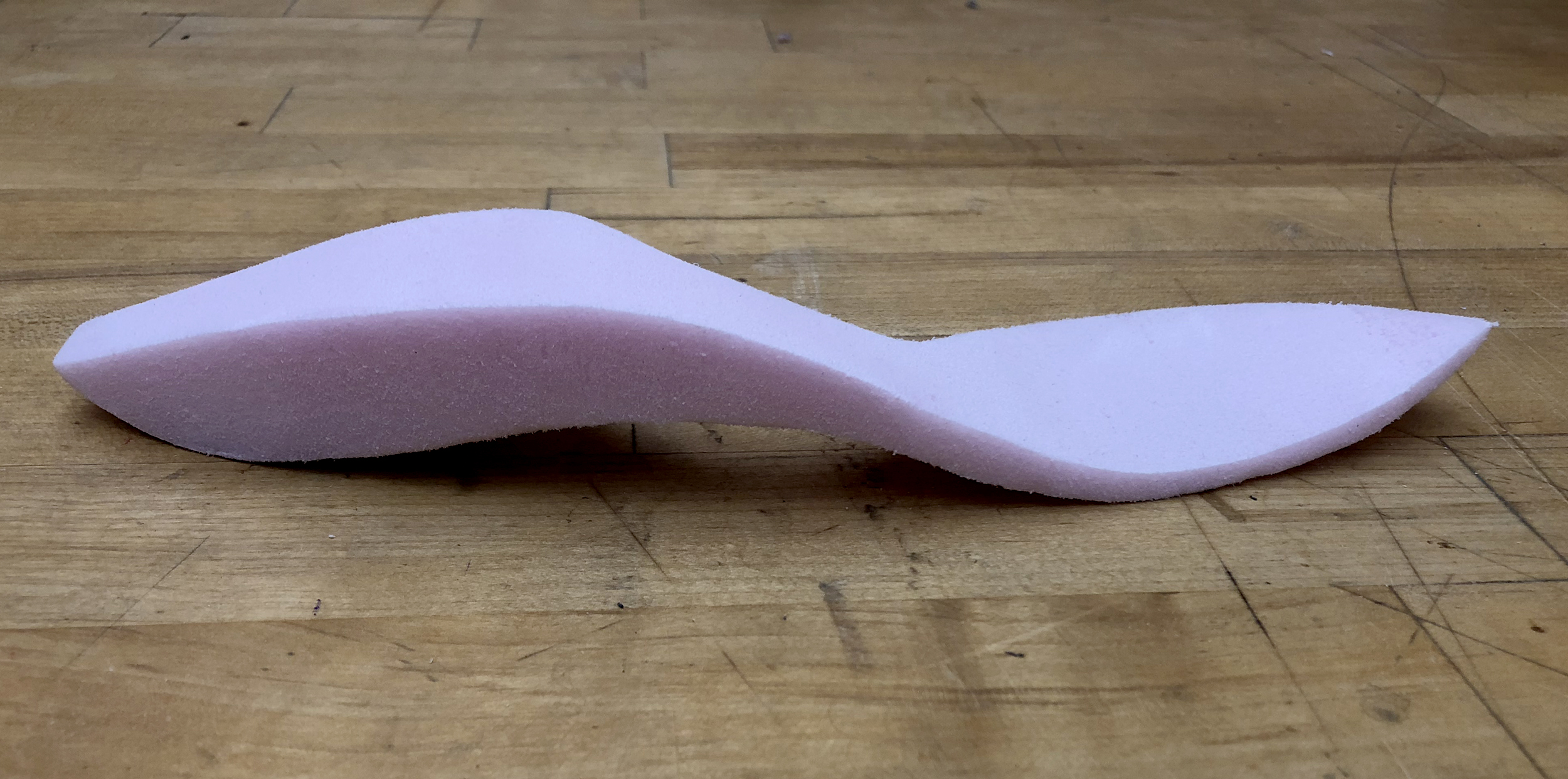

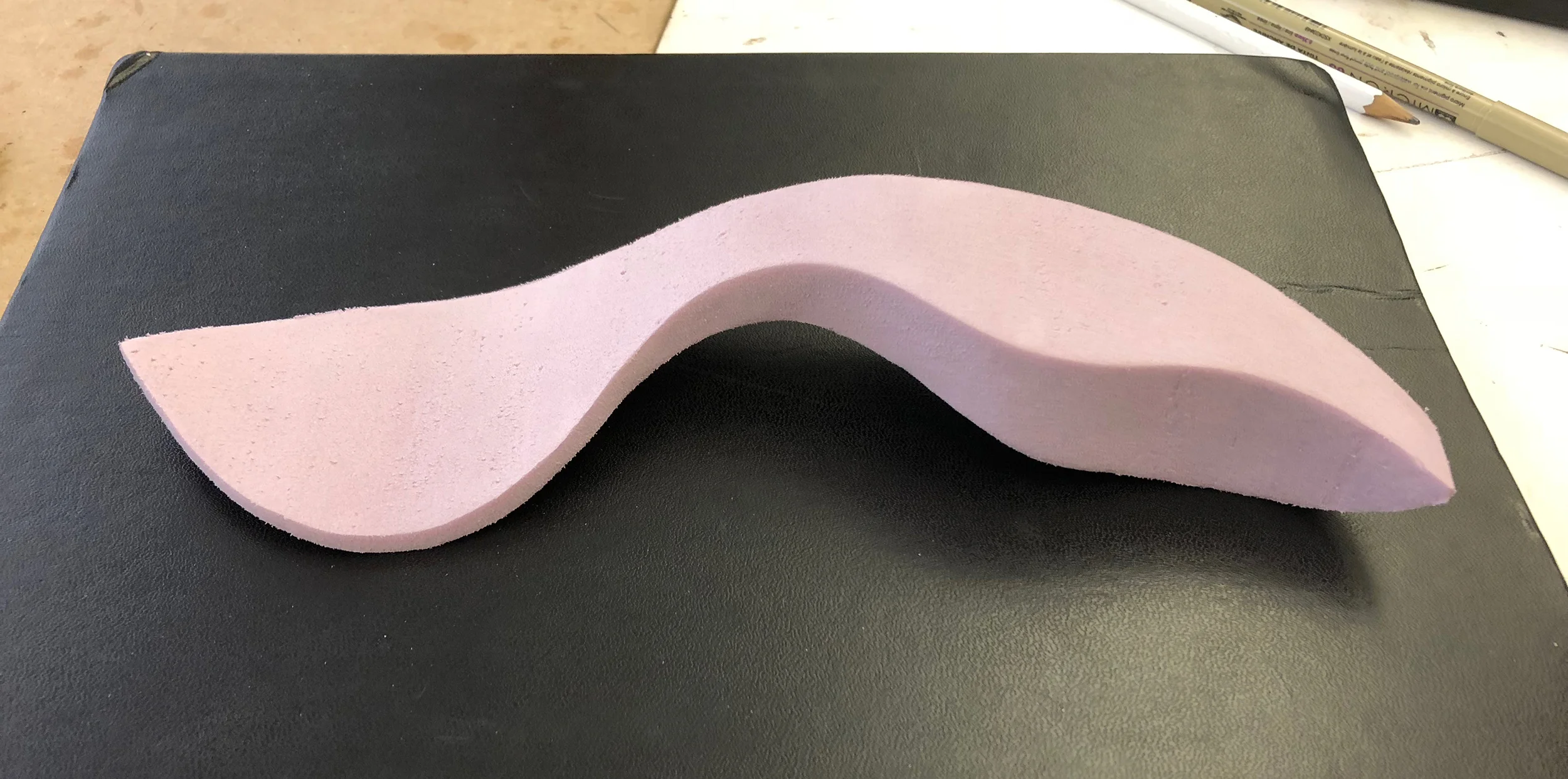
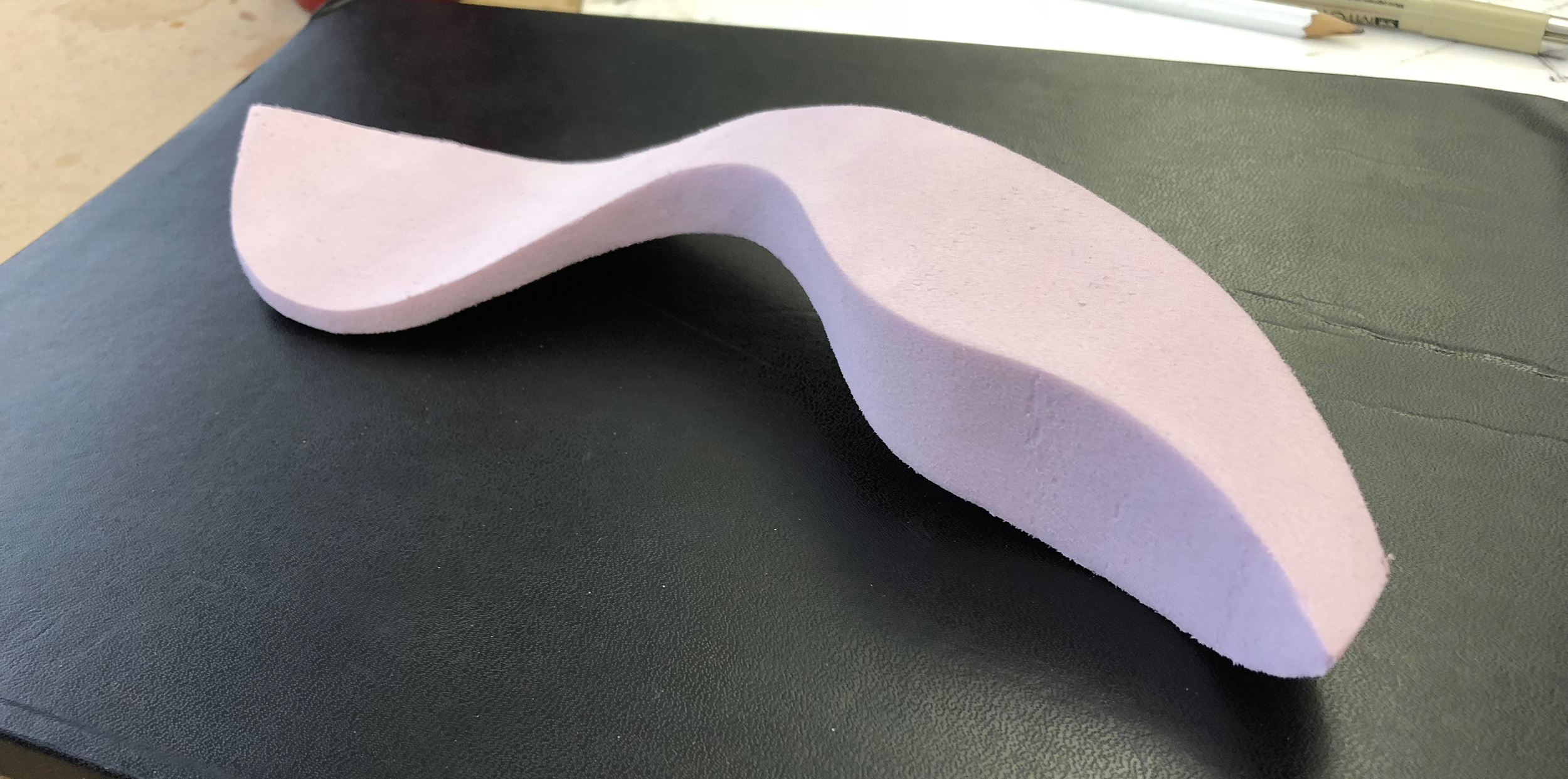
After receiving feedback that the shape of the handle was too ambiguous, I responded first by seeing how I could use secondary shaping to improve the form. I removed some of the material from the main bulge of the handle, opening up space in the middle. This allowed the hand to curl into a grip more naturally.
Moving forward with the information I learned from the previous model, I returned to doing loose sketches of profiles. Returning to this exercise with new insight about my form yielded interesting results.
I settled on the above design for my next iteration. The handle of this form is longer, slimmer, and better indicates to the user how to hold it. I continued to make adjustments even after putting the template onto the foam block, and then made the model below.
Refinement
For my final foam model, I sought to push the dynamic qualities of the design just a little further. I gave the blade more area, and lengthened the handle by making it curve more dramatically. I also made the side profile much thicker, so I could sand the blade down to be at an angle to the handle. Finally, I added secondary shaping, making the upper inside edge of the handle transition into the top of the blade—this was an important addition, as it marked a clear landing point for the thumb and furthered the aesthetic qualities of the design.


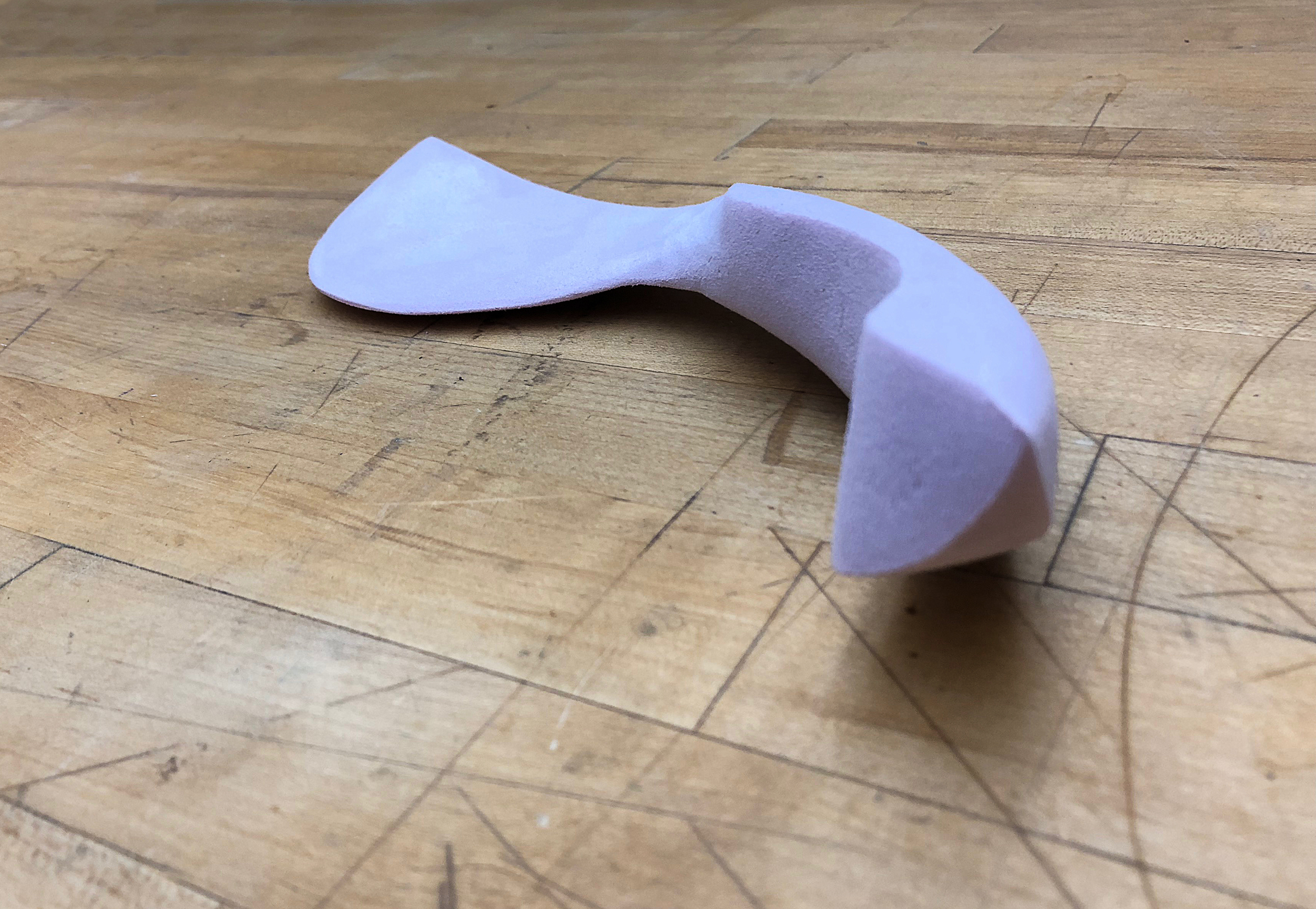
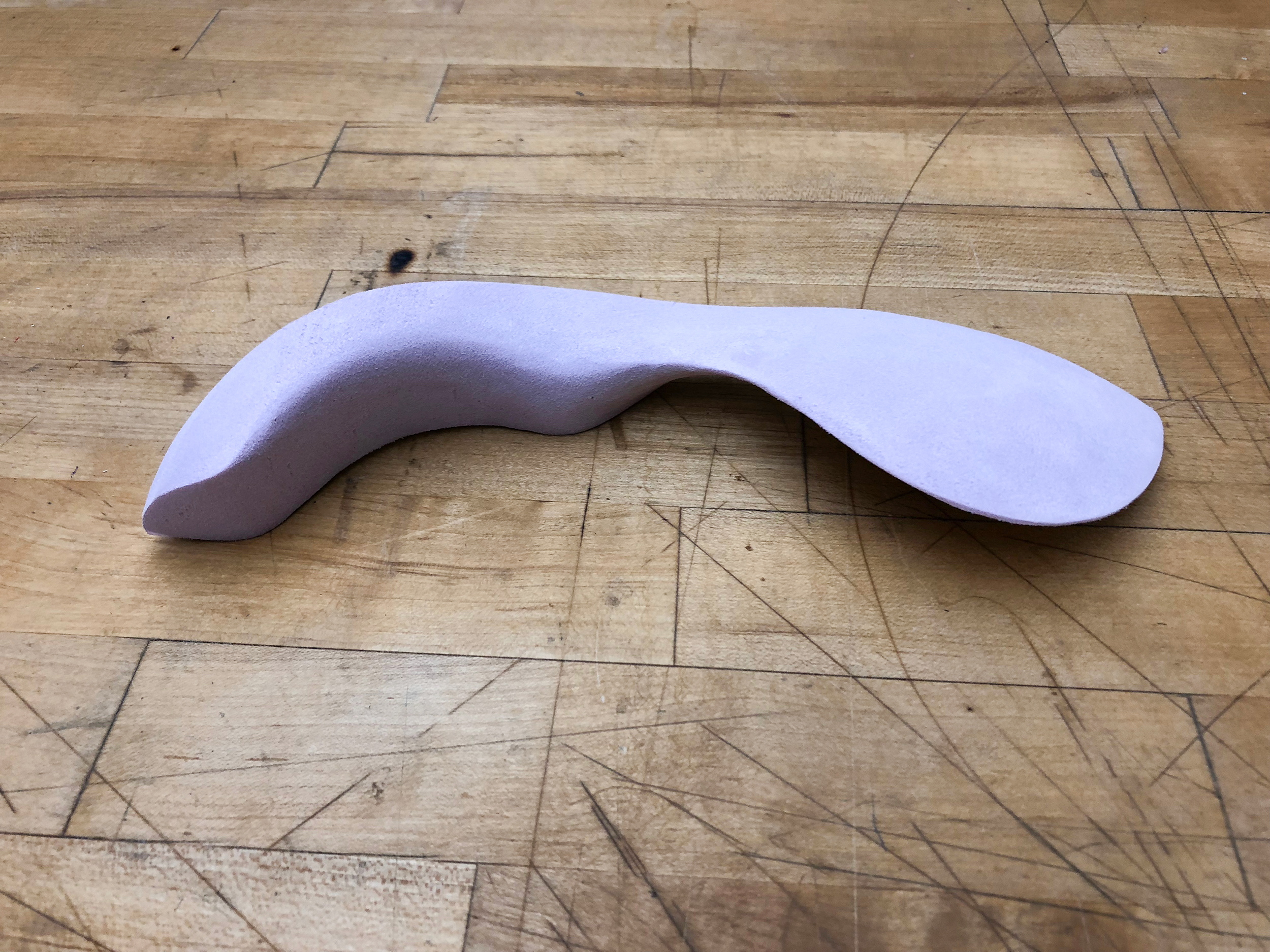
Before making the tongs out of wood, I did some final sketching of the form and visualized the steps of the fabrication process.
Fabrication
I began by laser-cutting my final templates on acrylic, and then tracing them on the wood blocks. Once again, I made the four cuts on the bandsaw, and then used a disc sander and spindle sander to shape the forms. Along the way, I added a new edge to the inside of the handle that resolved any remaining ambiguity about where the pointer finger was supposed to land. After refining a few other curves and transitions, I finished with some hand sanding to smooth out the surface.
Final
The final objects emphasize functionality through their form and fit in the hand. They communicate intended use effectively, and have a cohesive visual language that flows well.